From safety point of view it is essential to carry out strength and stability calculations of ships during loading operations. To make these calculations by hand without using a Computer is difficult, time consuming and open for mistakes. Since February 1998 International Maritime Organization (IMO) obliged ship owners to accommodate a computer and relevant software application able to carry out strength calculations for bulk carriers having length above 150 m. Afterwards this regulation was expanded on 1st of July 1998 under the scope of the rule coded as IACS UR S1 for all ships having length above 65 m. With the rapid proliferation of personal computers and obligation to make longitudinal strength calculations by computers, ship masters have been willing to use software applications also for stability calculations.
Delta Marine together with its solution partner Mesh (Mesh Engineering & Software Co.) provides a ship loading software which would meet precisely the requirements of the customers. Named as DeltaLoad, this software application is customized based on particulars of the ship such as type, dimensions, compartmentalization, etc. Basically DeltaLoad is a tool to carry out draft, trim, list, longitudinal strength, intact and damaged stability calculations interactively with the user as result of virtual loading operations of standard loads (ballast, fresh water, fuel oil, lubrication oil, etc.) and nonstandard loads (cargo). In the meantime documents and information such as draft survey report, loading report, hogging/sagging calculations, loading/unloading optimization can be produced using the software. DeltaLoad is also capable to present integration interface to many different tank level measurement systems to get tank filling level information constantly online.
DeltaLoad is a software product which can respond the request for digital intact and damaged stability calculation in ships either operated or chartered by to major oil companies, meet the requirement to run online and integrated with the tank level measurement system in parallel with the technological improvements in automation applications and -especially for container ships- fulfill the need to use a software application for loading and automation operations in order to maximize the amount of cargo and maintain close cooperation with container terminals.
Data Entry
The loading data can be entered manually from the compartment list or from the selected compartment in the graphical interface. In case that an electronic tank measurement system exists on the ship, it is possible to establish a communication link between this system and DeltaLoad via an online communication add-on module that ensures the interaction of two systems through the exchange of data either at desired times or continuously.
Intact Stability
When a loading data is changed in a compartment DeltaLoad is able to calculate automatically the new equilibrium status (as draught, trim and list) of the ship. The compliance of the criteria, which is calculated from the static stability curve, is checked with IMO criteria.
Container loading software minimizes freight costs and time wastes that used to go in developing cost-effective load plan bids for clients and customers. It easily gets harmonized to the most diverse load planning needs and improves efficiency by enforcing stringent loading policies and procedures. Create a load plan in seconds - Ship less air! Our container, truck and pallet loading software is trusted by the largest forwarders, manufacturers and airports. Start a free trial now! Create a loading plan for your truck or container free of charge now. The full version from PackApp has many other features to help you plan your loading. An option giving big savings is the possibility of checking which smaller vehicle or container will carry a given load and how much free cargo space is left. Carriers Information about free space and axle loads helps plan an added load.
Damage Stability
The compartments that can be damaged according to the damage standards determined in Marpol or IBC Codes are automatically damaged at given loading condition and the criteria are checked for every damage case. This feature provides damage scenarios without any requirement of expertise about damage stability on user side.
Longitudinal Strength
When a loading data is changed in a compartment, the new equilibrium status (as draught, trim and list) is automatically calculated and weight and buoyancy distribution is generated according to the new condition. The load distribution is calculated from the difference of weight and buoyancy distribution. Calculating the integral of the load distribution gives the shear force while calculating the integral of the shear force gives the bending moment. The calculated shear force and bending moment values are compared with the allowable values given by the classification society for the control points.
Container Loading
A special loading editor and reporting tool is provided for container loading. The loading cases can be provided in standard “EDI” format in order to be used in the ship and/or by loading ports.
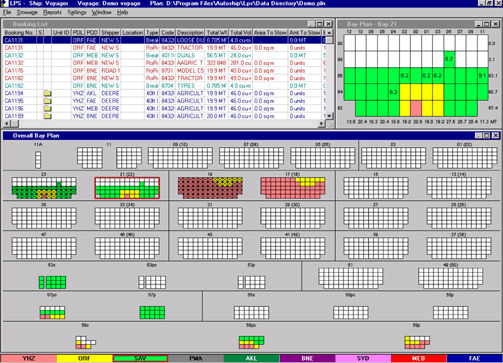
References
Optimizing Load Patterns – Litco Can Help!
Get a Complete Blocking / Bracing / Dunnage System FREE for Your First Load,
Plus Optimized Load Planning Diagrams
Our FREE Load Optimization Software Service puts you in control to comply with regulations in loading intermodal cargo containers for over-the-road trucking and railcar transit. With an optimized load diagram built using TOPS software, Litco’s shipping experts can help you maximize cubic feet per load while minimizing the costs of inflatable and cardboard dunnage, keeping your products safe, secure and damage-free.
Your First Shipment Travels with FREE Void Fill and Dunnage Products from Litco’s Advanced Product Damage Prevention Toolset
Experts in Load Optimization and Damage Prevention
[iphorm_popup id=”11″ name=”Load Optimization Request (Dunnage) – with Sample”][/iphorm_popup]
The number one reason for returned goods is damage caused by insecure, unstable packing in intermodal shipping containers or trucks. Effectively distributing the weight and volume of a load involves planning for empty space and effectively bracing your cargo to avoid damage caused by unblocked cargo shifting while in-transit.
Even palletized loads that seem stable, will lean or fall over in the trailer based on lateral forces (side-to-side shifts) put on cargo during transportation. Optimizing the loading pattern of your SPECIFIC FREIGHT whether you ship via 53 ft. trailer, railcar or intermodal container, means juggling 3 separate issues:
- Properly distributing weight within the trailer
- Maxing out the cubic volume allowable based on the weight limitations
- Ensuring sufficient and appropriate dunnage and void fill to effectively block-in and brace the cargo against shifts that will occur during transit and in handling.
In addition to product damage, disastrous accidents can occur if freight shifts while in transit. For this reason, the American Association of Railroads (AAR) develops regulations (download a free copy of their current requirements for blocking and bracing cargo in intermodal containers here) to stipulate how dunnage is to be used when packing containers that will be transported by railcar.
Weight as the First Consideration
When filling an intermodal container or truck with palletized product or other unitized loads, there are several variables that affect your optimized loading methodology. The first and likely most significant variable is weight. If the product you are shipping is heavy, the capacity of the trailer or container will limit your loading options.
A typical (empty) trailer with tractor attached, including diesel fuel weight can be about 35,000 to 36,000 pounds.
The maximum legal gross weight to drive without any special permits in the US is 80,000 pounds.
This means that a full truckload could carry 44,500 pounds max cargo weight. This weight calculation needs to include product, packaging, dunnage and pallets. If being conservative, it may be helpful to calculate based on about 42,000 pounds, allowing for an extra 1,500 pounds over product weight.
PRO TIP: If you are looking for a lighter-weight pallet, economical enough to use for one-way shipping and ISPM 15 (export-ready) compliant, check out Litco’s molded wood pallets.
Weight considerations for shipping intermodal
Maximum Weights, Weight Distribution, and Center of Gravity
A. The load weight must not exceed the limit as stated on the manufacturer’s plate. Combined weight of trailer and lading may not exceed 65,000 lb.* Combined weight of container and lading may not exceed the weight specified below for the length of container being loaded:
*Maximum weights as defined in current AAR Specification M-931-04 for trailers (effective 2/1/04 and subject to revisions thereto.
**Maximum weights as defined in current AAR Specification M-930-08 for containers (implemented 10/2008), and subject to revisions thereto.
B. Lading weight in trailers or containers must be evenly distributed both crosswise and lengthwise, and combined weight of lading and trailer or container must conform to all federal, state, provincial, and local regulations and transportation service requirements used at origin and to final destination. (See Illustrations 1, 2, 3, and 4.)
C. Combined center of gravity (measured from top of rail) of car, trailer or container, and load is not to exceed 98 in
Weight Distribution is Critical. Loading a trailer so it will not be overweight on any axle
The problem OTR truckers most often run into is not the total gross weight being over 80,000 – it’s having the truck loaded improperly so it is overweight on one of the tandem axles.
Part of the TOPS program helps your warehouse truck loading team properly distribute the cargo from front to back in the trailer based on weight.
As a starting point, it is important to know 3 things:
- How much does your load weigh?
- Does that include the pallets and packaging?
- How many pallets will comprise the whole load?
Container Loading Software Freeware
NOTE: If your trucking company is stopped for illegal weight distribution – even if the entire load is below weight limits – the shipment will need to come back to your warehouse for a re-load causing extra unpaid work for both the manufacturer and the trucking company.
Step-by-Step Truck Load Diagrams, Pallet Configuration
By inviting a Litco damage prevention expert in to work with you, you are getting access to industry-leading load configuration toolset created by TOPS Engineering. MaxLoad Pro is a cargo load planning, container loading, freight calculation and cube optimization software. It can calculate accurate container and truck load plans by determining ideal ways to palletize your goods, and using intelligent loading algorithms and extensive stacking rules develop a plan for you to follow so you can load mixed sized products into containers and vehicles.
AN EXAMPLE: One technique that can help create a more stable load and economize on space is loading pallets in a pinwheel configuration. Because the pallets most frequently used measure 40″x 48″ sometimes in a 96″ wide trailer you can turn one of the pallets 90 degrees, allowing two pallets to fit next to each other, hence the term “pinwheel.” Pinwheel loading creates additional stability by interspersing pallets with different load orientations.
Container Loading Software For Mac
Get a Complete Blocking / Bracing / Dunnage System FREE for Your First Load,
Plus Optimized Load Planning Diagrams